UKBIC opens new advanced Battery Development Laboratory
The UK Battery Industrialisation Centre (UKBIC) has opened its new upgraded and extended Battery Development Laboratory (BDL) which has greatly increased the facility’s capabilities in key areas of battery materials characterisation, cell analysis and forensic activities.
The new laboratory allows customers from all over the world to come to UKBIC to have their materials and cells analysed and tested in real-time. The enhanced capability will provide vital data to customers during the lifespan of the battery cell scale-up journey.
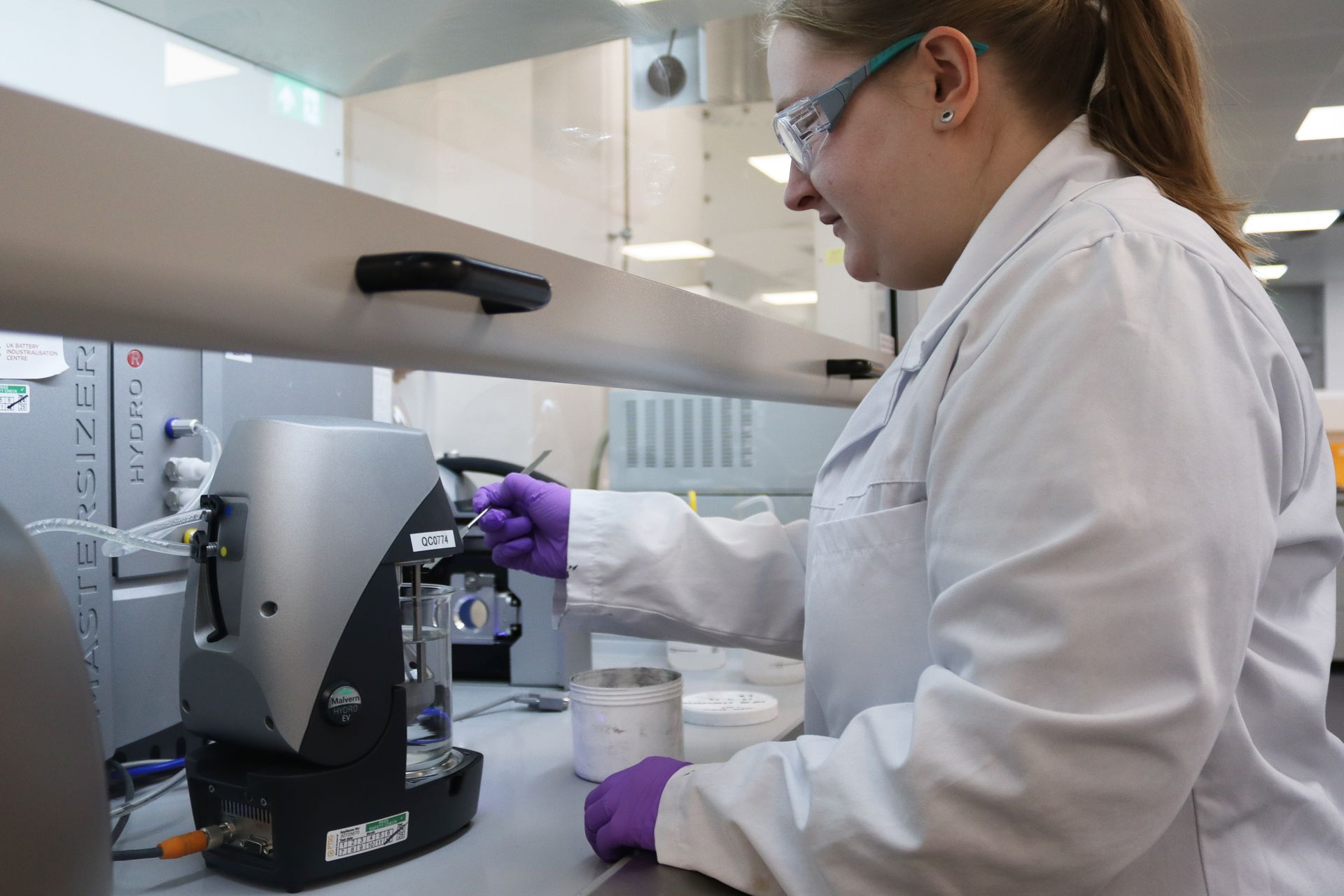
The 240m2 laboratory is open to all clients and will enable precision characterisation of products that are processed on the facility’s existing volume manufacturing line, the new flexible development line once it is operational, as well as those products brought into the facility from elsewhere.
The lab’s capabilities have five key areas for manufacturing development:
- Characterisation – for analysis including material properties such as morphology, crystal structure, elemental and material compositions. The lab contains equipment for elemental analysis (ICP), electrode imaging and particle morphology (SEM/EDX), phase analysis for crystalline materials (XRD), thermal properties and thermal stability (TGA), carbon-based materials characterisation (Raman), and electrolyte characterisation (GC, NMR).
- Chemical and physical processing – for the preparation of samples for characterisation and the handling of more hazardous samples. Equipment supports Quality Control (QC) analysis and the safe handling of electrode materials and water-based slurry. There is also a protected bench space for handling electrodes and a double glovebox for coin cell assembly.
- Forensics – equipped with both thermal and optical cameras for investigating cell failures and for the safe teardown of cells. Highlights include a VHX Microscope (Keyence), which has up to 6,000 magnification and which is capable of taking 2D and 3D measurements, a glovebox (MBraun) and a Shadowgraph (Keyence) microscope with automatic dimension measurement system.
- Electrochemistry – for advanced electrochemical analysis on coin cells, single-layer pouch cells and multi-layer pouch cells, including extended cycling and electrochemical impedance spectroscopy.
- CT Scanner – for non-destructive analysis of cells to understand issues and potential failure modes without the need to physically teardown the cell. The capability is a strategic partnership between UKBIC and Waygate Technologies.
The BDL is the second in a series of £74m upgrades to UKBIC to come online. Funded through the Faraday Battery Challenge by UK Research and Innovation, other enhancements are:
- Cell cyclers and environmental chambers to enable developers to continuously charge and discharge cylindrical and pouch cells, and measure how many cycles a battery cell can deliver over its life, which came on line late last year;
- A clean and dry zone where customers can rent space for their own development and testing purposes under strictly controlled environmental conditions, which is due to open this year; and
- A flexible pilot line where customers can undertake early-stage optimisation cycles and production trials at a smaller scale than UKBIC’s existing volume line.
Richard LeCain, UKBIC’s Chief Technology Officer, said: “Having this new on-site resource will ensure customers have a steady flow of data as they develop and scale new manufacturing processes, materials and chemistries as they head towards commercial production. This in-house capability will be an incredible resource for UKBIC and the UK battery industry.”
UKBIC is part of the Faraday Battery Challenge, which is a £610m investment programme which supports world-class scientific technology development and manufacturing scale-up capability for batteries in the UK.  The Challenge supports world-class scientific technology development and manufacturing scale-up capability for batteries in the UK.
-ends-
Notes to editor:
To arrange an interview, please email richard.robinson@ukbic.co.uk or phone +44 (0) 7503 628892
UKBIC is the UK’s national manufacturing battery development facility, providing manufacturing scale-up and skills for the battery sector.
The purpose-built facility is where businesses develop their battery manufacturing processes at the scale they need to move to industrial production and where those working in the industry can develop new skills by working on the production line, alongside UKBIC’s specialist teams.
Created with an initial investment of £130m, an additional £74m has now been committed by UK Research and Innovation to enhance the facility by installing a new pilot line to bridge the gap between UKBIC’s larger scale offering and small-scale demonstrators available elsewhere. Funding is also being used to support the construction of a new battery development laboratory, a clean and dry zone, and cell cyclers.
Opened in July 2021, the Coventry-based facility can be accessed by organisations with existing or new battery technology, or companies looking at entering the industry. UKBIC doesn’t retain customer IP.
UKBIC’s construction was part-funded through the West Midlands Combined Authority and was delivered through a consortium of Coventry City Council, Coventry and Warwickshire Local Enterprise Partnership and WMG, at the University of Warwick.